取樣、制樣質量對直讀光譜分析結果的影響
現代冶金工業(yè)的精煉、連鑄及連鑄連軋技術的快速發(fā)展,在提高產品質量、增加品種、降低消耗、增加效益方面要求越來越高,光電直讀光譜分析作為種成熟的分析技術起著越來越重要的作用。直讀光譜分析具有操作簡單、速度快、適應品種多、能進行多元素同時測定、提高效率等特點,但對直讀光譜分析而言,樣品的均勻性及代表性是至關重要的。因此,必須重視取樣方法及其樣品的處理。如果忽略這一問題,將會嚴重影響分析的精度和準確性。

大型鋼鐵公司煉鋼成品試樣、精煉爐微調樣品及其它過程樣基本上已全部采用真空直讀光譜儀代替濕法化學分析,而且全部為在線和臨線分析,大大提高了分析速度。光譜試樣不僅要有良好的代表性,而且分析表面應均勻一致,樣品制備后無氣孔、砂眼、裂紋及夾雜等。一般來講,所取分析試樣為乒乓球拍或圓柱形狀。由于種種原因,樣品(特別是中高碳鋼試樣)表面時常存在氣孔及砂眼等缺陷現象,按分析要求,不合格試樣不能分析,勢必會影響生產節(jié)奏;如果勉強在不合格試樣上分析,質量將得不到保障,而且留下用戶質量異議的隱患,重新制樣將形響后續(xù)軋鋼生產。因試樣不合格需要氣割補送樣,增加分析時間、人力及材料消耗成本;對此,我們針對對試樣存在的氣孔及表面砂眼等缺陷現象進行分析驗證,探討了砂眼及氣孔形成的原因,重點是對分析質量的形響進行了細致的分析,提出了應對方案。同時,也對制樣過程中的影響因素進行了研究。
2 實驗部分
2.1實驗方法
選擇一定量的表面有氣孔的高碳及低碳鋼試樣,用直讀光譜儀進行測定,再將樣品鉆取屑樣用化學方法及紅外碳硫儀分析,將兩種數據進行統(tǒng)計比對分析。
2.2 缺陷試樣的分析
數據見表1?;瘜W分析為紅外碳硫儀結果,其他均為直讀光譜儀分析數據。

2.3對用直讀光譜儀分析的376組數據合格率進行統(tǒng)計
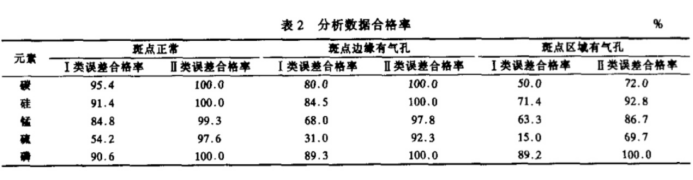
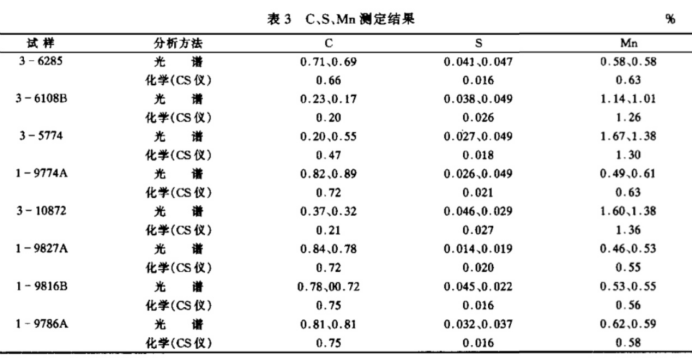
(1)從表2、表3的統(tǒng)計結果可以看出,當試樣存在砂眼或氣孔時,對C、S、Si、Mn均有較大的影響,其中對C、S、Mn的影響*大,S的準確性*低,Ⅰ類誤差合格率僅為15.0%;當試樣表面有氣孔或裂紋時,即使激發(fā)斑點正常,S的準確度也較低,雖然Ⅱ類誤差合格率能達到90%,差值仍在0.004%~0.008%左右,離工藝要求還有相當的距離;當激發(fā)斑點區(qū)域有氣孔或裂紋,根本談不上正常進行分析,這是因為光諧儀在激發(fā)這類樣品時發(fā)光不良或根本不發(fā)光,試樣有較大孔洞或裂紋時,還會引起光譜儀光源開關跳閘。因此,取樣是否合格,是試樣能否進行光譜分析的首要條件。在分析時,發(fā)現樣品有較多的氣孔、大的孔洞或裂紋必須重新取樣。
(2)對高碳鋼的氣孔樣進行統(tǒng)計。結果表明,取樣器含鋁絲與試樣是否形成氣孔有一定的聯(lián)系,含鋁絲取的樣有氣孔的相對要少得多,部分存在明顯氣孔的試樣一般不含鋁絲,當然這不是絕對的;在一段時間內,所煉鋼種為低碳鋼時,用含鋁絲的取樣器仍有部分試樣有氣孔,列舉的大個氣孔試樣中,就有兩個為低碳鋼。建議取樣時盡量采用含鋁絲的取樣器以減少氣孔樣的產生。
(3)關于取樣氣孔成因及采取的相應措施。取樣時,將取樣器伸入鋼水中,在負壓作用下,鋼水沿石英管進入取樣器,充滿其內部,經冷卻結晶成形,成球拍狀試樣。取樣器一般用鋁絲或鈦作脫氧劑,防止進入取樣器中的鋼水遇氧作用,生成夾雜物。液態(tài)鋼水冷卻凝固時體積縮小,如果冷卻速度過快就容易形成氣孔。為了使取好的試樣盡可能快地發(fā)送到化驗室,生產操作人員通常采取急速水冷方式,試樣淬火,容易導致難磨及試樣內部形成裂紋。有關資料表明,低碳鋼可將紅熱的樣品放人流水中急速冷卻,樣品組織結構形成馬氏體或貝氏體鋼,保證碳等元素的分析準確度。高碳鋼直接用水急冷易出現裂紋,應采取氣冷后再用水冷的方法,防止產生裂紋。
取樣過程中,影響取樣質量的因素有:取樣時鋼水的溫度;取樣器伸入鋼水的深度;操作的速度;成形試樣的冷卻速率等。因此,取樣時需注意以下事項:
a)取樣時鋼水的溫度高,鋼水的粘度相對較小,流動性好,易充滿取樣器,且時間相對較短,可降低鋼水的氧化程度,避免形成夾雜或氣孔。
b)取樣器伸入鋼水的位量較深,鋼水成分均勻性好,鋼水溫度也高,吸入夾雜鋼渣的可能性較小,所取的試樣具備良好的代表性。
c)取樣操作速度快,鋼水沿石英管進入取樣器的過程中溫度下降的差值小,有利于試樣的成形。
d)成形試樣的冷卻速度要控制好。取好試樣后,采用急冷還是緩冷要根據品種情況而定。
總之,在取樣這個環(huán)節(jié)上,為了取得合格的試樣,不影響光諧分析的進度和精度,應加強光譜試樣的取樣培訓工作,制定相應的取樣操作規(guī)程,嚴格遵守操作規(guī)程。只有取得合格的試樣,才能確保分析工作的順利進行,確保生產各個環(huán)節(jié)的順利銜接,使產品質量和產量得到可靠的保證。
(4)制樣過程中的影響因素及采取的應對措施。氣孔樣在磨樣過程中,表面小氣孔大多數被掩蓋,不易觀察,激發(fā)后則較為明顯;在光譜分析中,激發(fā)后需要仔細觀察激發(fā)斑點區(qū)域是否有氣孔,決定異常數據的取舍;激發(fā)斑點重疊或部分重疊,結果也容易超差。
為了提高分析準確度針對氣孔樣的光譜分析,除了上述注意事項外,采取下列措施。
1)禁止在試樣上同一點重疊激發(fā),防止實測值偏低。
2)激發(fā)后仔細觀察,若在斑點區(qū)域或邊緣發(fā)現氣孔裂紋,應重新制樣或換位置澈發(fā)。
3)為防止出現判斷偏差,有少量氣孔的試樣需經過兩次以上磨樣,激發(fā)次數應不少于五次,正常有效分析數據不少于三點。
試樣表面基本沒有缺陷,激發(fā)斑點也正常,分析數據有時卻偏離正常范圍這就與制樣有關了。制樣時,樣品用砂輪或光譜磨樣機高速研磨時產生的溫度可能導致表面組織狀態(tài)的變化,因此試樣研磨過程中需要及時冷卻,磨制好的試樣表面紋路要保持一致,研磨要求有一定的深度,*好在0.3mm以上,如果研磨深度達不到0.3mm以上,分析結果波動很大,尤其是C、P、Si、Mn影響較大,其表現在爐前樣品日后再分析時,結果偏低,經多次研磨后至一定厚度后分析結果就穩(wěn)定的多。樣品自身溫度也有一定的影響,隨溫度上升分析結果也逐步上升,在實際分析工作中,樣品冷卻的時間一定要保證,可用帶水的濕抹布冷卻磨制好的樣品20s。分析時試樣溫度應在30~500℃之間。取一典型的012-337試樣進行冷卻試驗,數據見表4。

此外,分析人員應檢查儀器狀態(tài),包括真空、溫度、漂移系數,及時清掃激發(fā)架、電極,檢查氬氣流量、純度及氣流穩(wěn)定性等。管理部門加強管理,加大考核力度,提高化驗人員的責任心及技術水平,增強質量意識,嚴格執(zhí)行操作規(guī)程。
4 結論
(2)取樣是否合格,是試樣能否進行光譜分析的首要條件,取樣應嚴格遵守有關規(guī)定,只有取得合格的試樣,才能確保光譜分析的準確性,保證生產節(jié)奏。
(3)化驗工應嚴格遵守操作規(guī)程,將儀器狀態(tài)調整好。對于有缺陷如氣孔的試樣,必須要磨至試樣表面符合要求,仔細觀察激發(fā)后試樣表面狀況,嚴禁同一點激發(fā)試樣,數據有異常的,應及時別除,注意進行必要的比對分析。
(4)對于缺陷不能磨去的試樣,又不好重新取樣的,用鉆床鉆取屑樣,應避開氣孔及裂紋,防止取到夾雜物,用化學方法、紅外碳硫儀分析基本上能代表試樣的組成。